Efficient battery system development with the digital twin
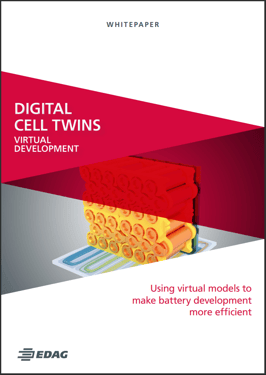
As suitable tools to understand the stresses on battery cells in electric vehicles during crashes and during operation were not available until now, developers played it safe. They planned generous buffers and designed robust housings to protect the battery cells from all conceivable dangers.
Obviously, this approach is not very efficient. EDAG Engineering has therefore taken up the issue and looked for ways to optimize development. As a result, the engineering specialist developed a digital twin for battery cells. It is based on virtual models and simulations that have been verified and optimized in extensive test series.
The simulation of short-circuit behavior and electro-thermomechanical behavior closes a crucial knowledge gap in battery cell development. Now, the virtual model can be used to test stresses from a crash or the effects of normal operation, for example in the form of "breathing", i.e. temporary expansion during charging and discharging of the cells. This allows for more precise development, which saves material while maintaining the same level of safety, avoids oversized buffer spaces and thus creates potential for higher capacities. The EDAG SCALEbat, for example, achieved an increased range of over 50 percent.
Find out more about the development of the methods and tools and the potential of EDAG Engineering's digital twin in the white paper "Digital Cell Twins: More efficient battery development with virtual models", which you can download here.
Download White paper now
** EDAG Group: EDAG Engineering Group AG, EDAG Engineering GmbH, EDAG Production Solutions GmbH & Co. KG, EDAG aeromotive GmbH